CNC Press Brake CNC axis analysis
1. Introduction
The Press Brake is one of the common equipment in the metal processing industry. It bends the metal sheet into the required shape by applying force. It is widely used in automobile manufacturing, aerospace, construction and other fields. Traditional mechanical bending machines need to rely on manual operation and mechanical transmission to complete the bending process, which has problems such as low production efficiency and limited accuracy. The CNC bending machine uses CNC technology to control mechanical movement through computer programs to achieve automated and high-precision bending processing.
2. Press Brake usually have the following axes:
Y axis: (Y1 and Y2) The Y axis usually controls the vertical movement of the upper mold. By controlling the position of the Y-axis, the lifting and lowering of the upper mold can be adjusted to control the bending angle and shape accuracy.
X-axis: (X1 and X2) The X-axis usually controls the horizontal movement of the Back Gauge. The rear gage is used to support the workpiece and determine the bending position. By controlling the X-axis, the position of the rear gage can be adjusted to achieve precise control of different bending positions.
R axis: (R1 and R2) The R axis is usually used to control the lifting movement of the back gauge and is used for bending some special workpieces.
Z axis: (Z1 and Z2) The Z axis is usually used to control the left and right movement of the back gauge and is used for bending some special workpieces.
V-axis: The V-axis is an important part of the CNC bending machine and can be automatically crowned to maximize the accuracy of sheet metal bending.
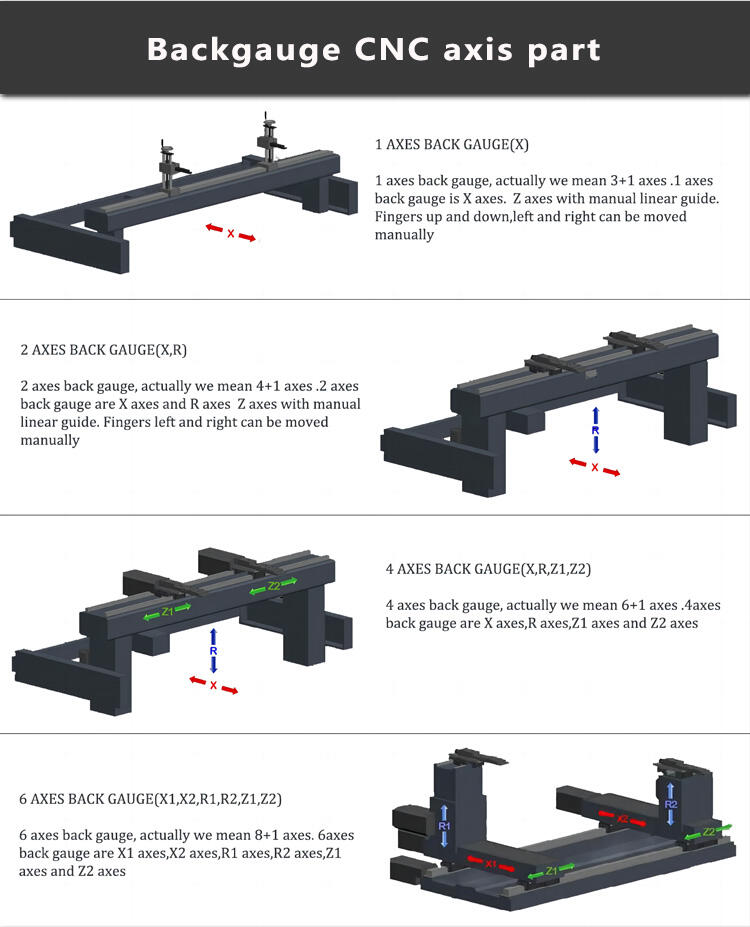
3. Working principle of CNC axis of bending machine
The CNC axis is a key component in the CNC bending machine. It realizes the calculation of all movements of the bending machine through precise computer control. CNC axes usually use servo proportional valves and motors as drive sources to achieve precise position control through encoder feedback and closed-loop control. CNC bending machines can be configured with multiple CNC axes to achieve multi-axis linkage and complete complex bending processing tasks.
4. Advantages of a Press Brake equipped with multiple CNC axes
(1) High precision: The CNC axis adopts a closed-loop control system, which can monitor and adjust the movement position in real time. It has high positioning accuracy and repeated positioning accuracy, and can meet the processing needs of high-precision parts.
(2) High efficiency: The movement speed and acceleration of the CNC axis can be adjusted according to the processing requirements, enabling high-speed and efficient production.
(3) Flexibility: By programming the motion trajectory and angle of the CNC axis, the CNC bending machine can flexibly realize the bending processing of various shapes and adapt to the needs of different products.
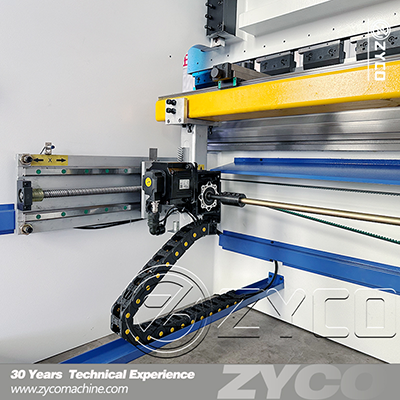
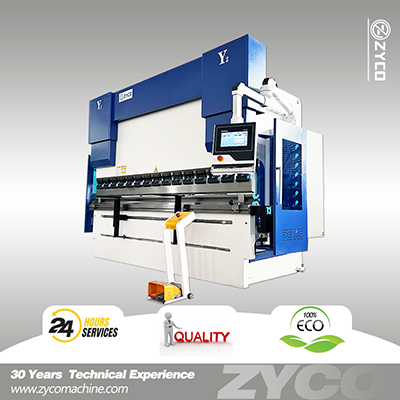
5. Development trends
With the continuous advancement of technology and the improvement of automation level, CNC Press Brake and their CNC axes will continue to develop. In the future, CNC axes will be more intelligent and have higher adaptability and learning capabilities. At the same time, the connection and collaboration with other process equipment and production lines will be closer to achieve the goals of intelligent manufacturing and industrial Internet.
Recommended Products
Hot News
-
Saudi Arabia-WC67K 100T 3200 NC Press Brake & QC12K-4x3200 Shearing Machine & 3x3100 Folding Machine
2024-11-11
-
USA-PANEL 1400PA3-DA BENDING CENTER
2024-10-28
-
Argentina-WC67K 125T 3200 CNC Press Brake & QC12K-4X3200 Shearing Machine
2024-10-25
-
Main uses and development of Bending centers
2024-10-24
-
Indonesia-WC67K-30T 1600/63T 2500/100T3200/160T 3200 CNC Press Brake
2024-10-21
-
How to deal with the lack of pressure in the Press Brake
2024-10-15
-
How to maintain a Press Brake: 28 tips to keep the Press Brake in perfect condition
2024-10-04
-
Mexico WC67K 80T 3200 NC Press Brake & QC12k-6×3200 Shearing Machine
2024-09-26
-
Comprehensive Guide to Bending Forming
2024-09-26
-
Welcome Indian customers to visit our factory
2024-09-23